Building Sustainability
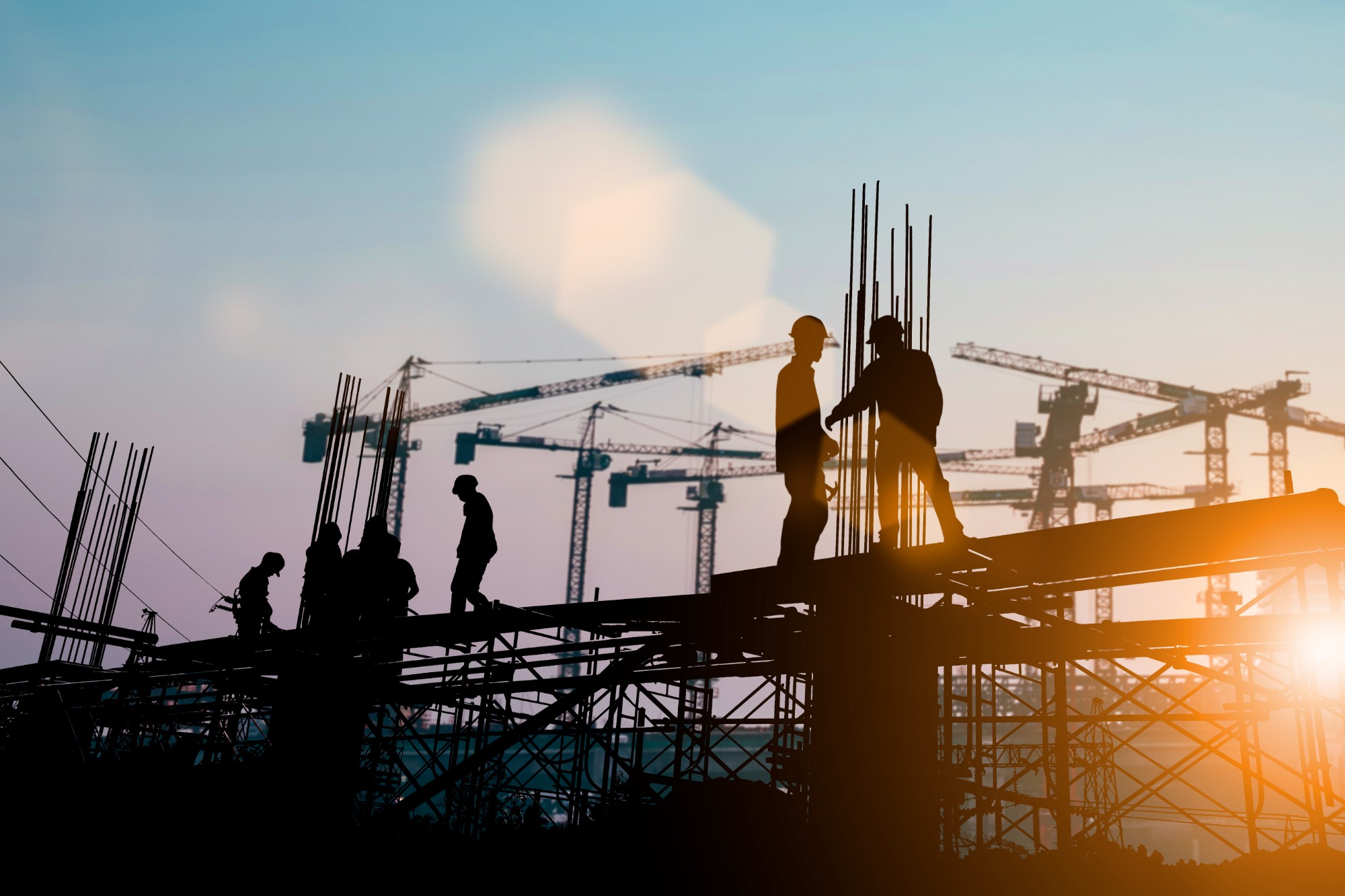
The idea of changing the world seems like an impossible task until, like anything else, you begin to look at your personal impact and see what you can achieve. As the owner and operator of a large precast manufacturing construction company in Guelph, ON, Kiwi Newton Group, my passion for environmental sustainability may be hard to understand. When it comes to environmental sustainability, the construction industry holds an important role to play in this, specifically with building sustainably. Materials, technology, architecture, technical design, and site time are all factors that can affect a structure's overall footprint, and it is our responsibility as an industry to do what we can to lower this impact.
Why Building Sustainability?
The construction industry is responsible for emitting approximately 11 per cent of global carbon emissions due to embodied carbon in the manufacturing of the building materials, and for 28 per cent of the world's carbon emissions due to the energy use of buildings post-occupancy. Governments around the world, including Canada, have made promises, and set goals to reduce their carbon emissions, and organizations such as the Green Building Council of Canada are urging companies to find ways to lower their carbon footprint. The National Engineering Policy Centre has stated the industry must reduce its carbon emissions by 78 per cent before 2035. Adapting to new technology and building methods will play an integral role in the transition towards lower embodied carbon and lower energy use in buildings. As new and current buildings continue to move away from carbon to non-carbon emitting systems, the task of achieving net zero energy use will become easier and more accessible.
An important goal for our organization is to develop buildings that meet the environmental targets set by world leaders and various authorities. Using innovative building systems as the cornerstone, with the integration of advanced green technologies at the core, we are succeeding in our environmental endeavor. A current example of this work includes planning further measures to lower the embodied carbon in the manufacturing of concrete and fabrication of steel. Measures like these will assist our clients in meeting environmental requirements for their new buildings, save capital costs, and reduce operating costs.
Concrete as an environmentally sustainable material
As an incredibly durable building material, concrete creates structures that are built to last. Concrete is noncombustible, more resistant to natural elements, and structurally solid. These factors of longevity must be considered when comparing the entire cycle of a building’s carbon footprint. Kiwi Newton Group designs using an integration of functions and disciplines, enabling the affordable delivery of buildings with a lower embodied carbon and reduced energy use. We continue to look for ways to reduce the carbon footprint of concrete from using less, to doing the same job but utilizing carbon dioxide treatment during the concrete manufacturing process. This produces higher quality concrete to last longer in its environment.
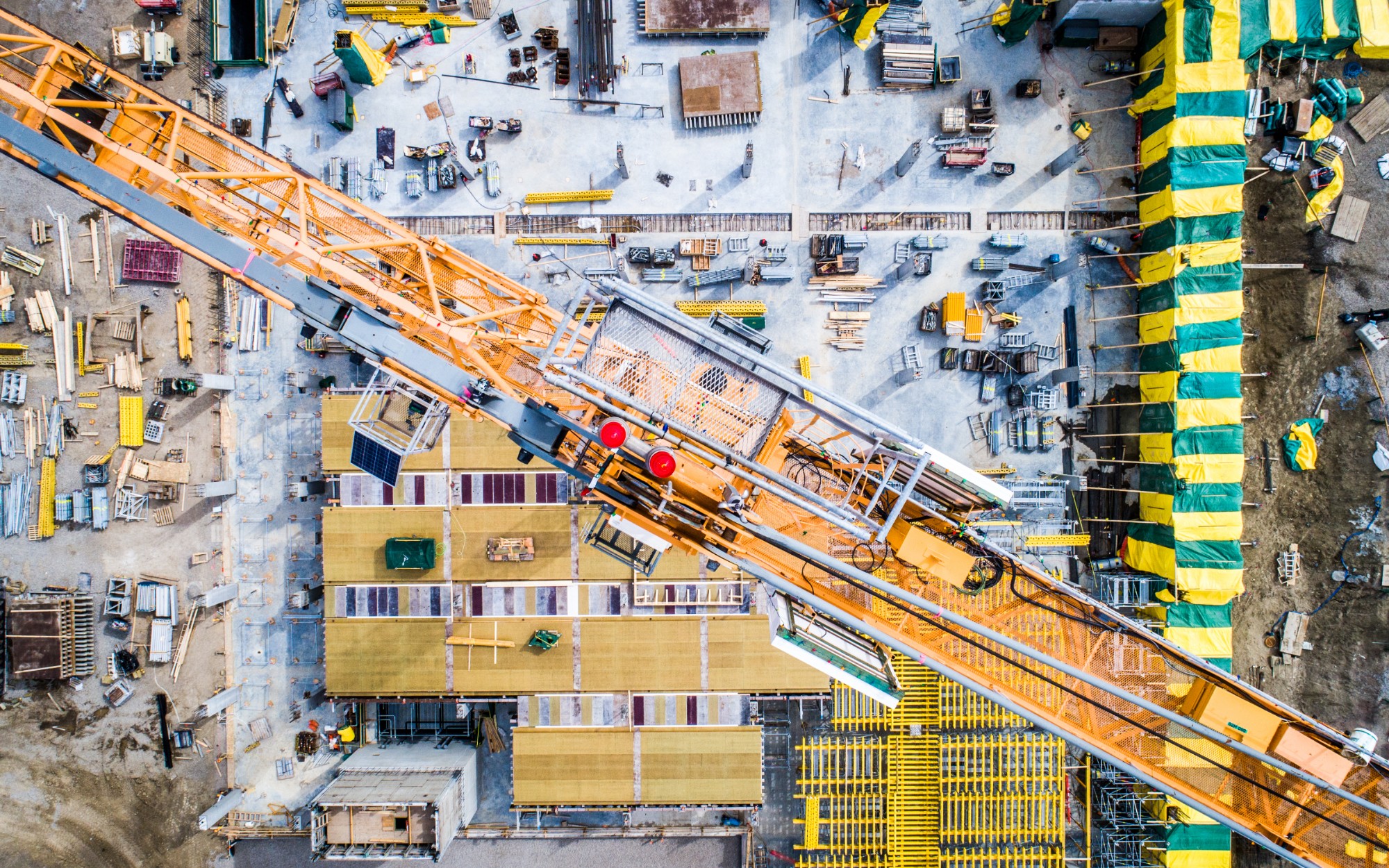
Solar Energy
As the movement towards green energy increases, solar power has been gaining momentum as property developers begin to see the benefits. Generating electricity through renewable solar power instead of electricity generated with fossil fuels can dramatically reduce emissions through the life of the building, while saving the owner operating costs. Energy prices are likely to increase as time goes on, making these investments more meaningful as the building ages. Localized power generation reduces draw on the power grid and reduces the need to invest in upgraded grid distribution, saving capital investment and curbing the increase in power costs.
Putting Ideas into Practice
Knowing all of this, our team has put these values into action and developed a system called “KiwiCondo Commercial.” This prefabricated system, can produce net-zero buildings that meet or exceed Passive House standards.
Passive House is the only internationally recognized, science-based, and proven energy standard in construction. At a basic level, a structure built to Passive House standards will employ good insulation and minimal thermal bridges. It will contain the well-designed use of solar, and internal resources, maintain high levels of airtightness, and have a ventilation system that provides efficient heat recovery along with good indoor air quality. The appeal of Passive House buildings is that they are built with airtight insulation that maximizes the use of natural heating systems, such as the sun, and consumes 90 per cent less heating and cooling energy than conventional buildings. The core principles behind this system are simple – ventilation by promoting natural ventilation through simple openings and mechanics to encourage cross-ventilation, minimal space heating, lighting and electrical control.
The KiwiCondo Commercial building system provides an alternative to traditional methods for building condominiums and commercial projects as the entire building is pre-designed and tailored to the specific needs of the client. All building components are factory-made, then shipped to site as an integrated element to be placed in in its location on the building. Various integrations occur including architectural, mechanical, electrical, and structural elements. Once on site, all integrated elements are erected and connected. Project completion times are shortened because of the integrations completed at the factory, ensuring high quality through factory-controlled manufacturing. The results are energy efficient, architecturally designed buildings, with all the advantages that associated with the controlled conditions of a factory-made product.
What makes this building system unique, is that it centers around inherent energy efficiency. Non-flammable, non-combustible insulation is installed to the exterior side of the precast concrete walls, all windows are thermally broken, and triple glazed for high performance, and these details provide continuous moisture and thermal protection. When the building is heated, the concrete acts as a large thermal mass, mitigating fluctuations in outdoor temperature and allowing the inside temperature to remain consistent. The thermal insulated concrete mass increased energy efficiency by 8 per cent by leveling peaks and valleys of temperatures during the day. The in-floor hydronic heating and cooling systems use thermal mass to provide temperature control to the building and utilizing the hydronic system for in-floor heating and cooling is more efficient than pushing hot air due to the energy draw on fan capacity.
Moving forward Sustainably
Ultimately, green energy will become the standard for all buildings, as it should be. As an industry, we have an obligation to our clients and the environment to find cost-effective green alternatives that don’t break the bank. Education will be important in this feat, as people need to understand not only what is available but how it will benefit them. Outlets like Building Good are an excellent way to start getting the message out and, once it becomes more known, I believe Passive House become the gold standard in building construction – and that is something to be excited about