Mirror Imaging: Embracing Digital Twins in the Buildings Industry
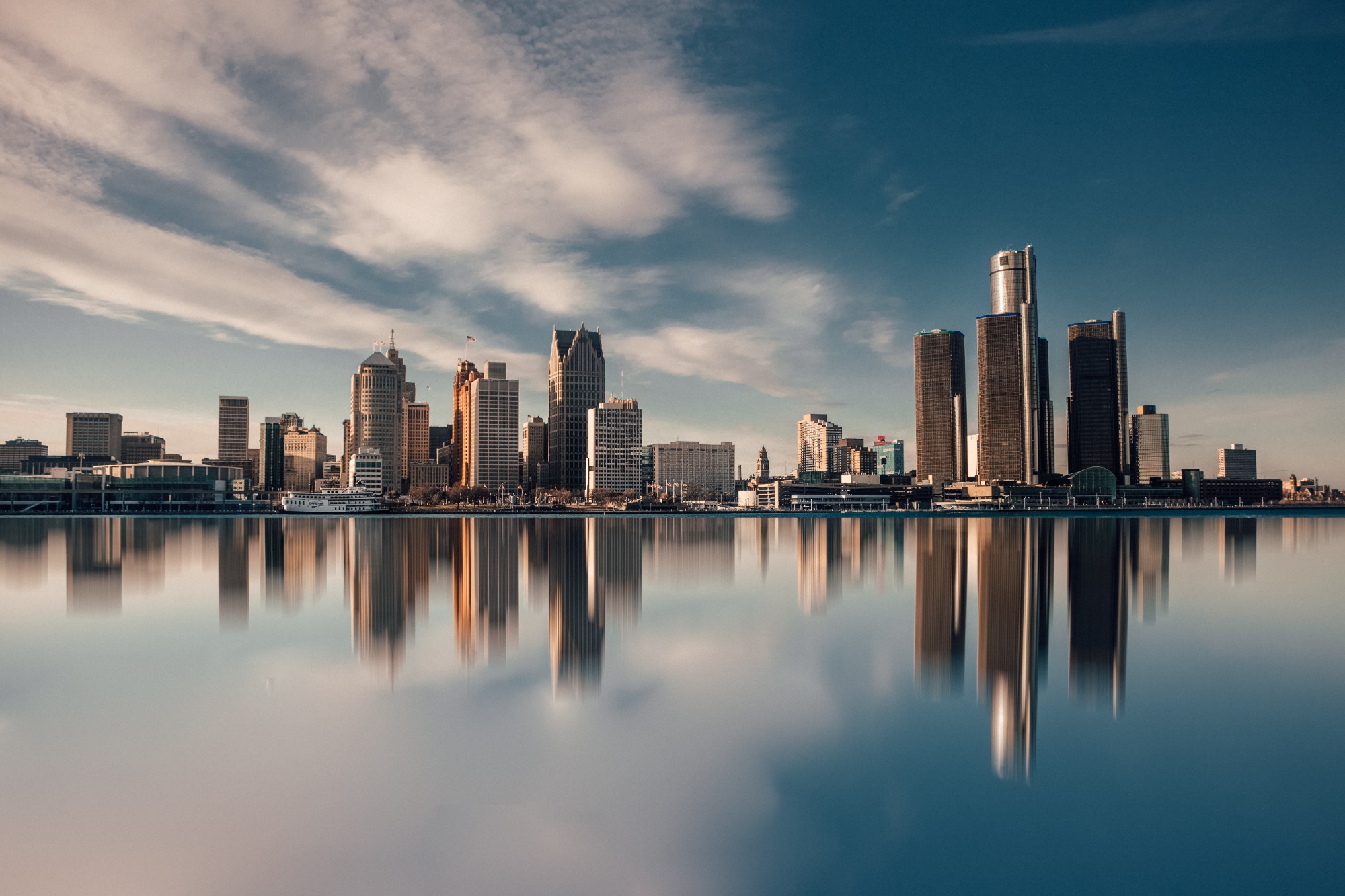
Forbes defines Digital Twins as the combination of IoT sensors, machine learning and cloud computing to create dynamic digital simulations of physical systems and processes (Source). It is essentially a digital clone of physical objects, systems, processes or environments that is identical to its real-world counterpart.
The concept of Digital Twins first took a practical shape when NASA applied it to a spacecraft in 2010 (Source). This concept has gained mainstream popularity and been applied by many different industries in a variety of ways.
We sat down with Mohamed Adel to discuss how he is seeing Digital Twins in the world of building construction and how companies can become Digital Twin ready. Improved safety, project tracking, project handover, and facility management are some of the key benefits the companies could gain from Digital Twins.
What is a Digital Twin?
A digital twin is a detailed, up-to-date digital version of a physical asset, process, or system. It includes data from the entire lifecycle of a building project, including design, construction, and operations.
In my opinion, a digital twin has three main parts:
-
Geometric and Associated Data: This includes the exact measurements and locations of assets within a building, such as an air handling unit's width, height, depth, and position.
-
Handover Data: Practical information associated with the assets at the project handover stage. For example, warranty details for equipment.
-
Real-time Data Feed: Information flowing from the physical asset to its digital counterpart, including commissioning and operational data.
It's worth noting that these components are part of a larger, more complex set of information that makes up a true digital twin.
What Does a Digital Twin Look Like?
In a 3D building model, you will see the rooms and spaces and also the sensors and where they are exactly located in the room. For example, you select an occupancy sensor above a door in a room, and it will show a red colour if it’s empty, but if it’s occupied it would show as green.
NVIDIA’s Digital Twin software (Omniverse) showcases a cool example of a Digital Twin for the BMW factory manufacturing facility. They were able to streamline the manufacturing facility and simulate every aspect of their manufacturing pipeline with this platform.
Benefits for Facility Management
The majority of the benefits will be for the building owner because while construction may be 2 to 10 years, in the actual facility life cycle it’s 50 to 100 years.
Currently, handover from construction general contractor (GC) to building operator is a painful process. Often times, data from PDFs, hardcopy documents, excel sheets, and more all needs to be manually transferred into the operator’s facility management software system. Even if the information is digital, there are typically different platforms that are incompatible.
In my opinion, Digital Twins are the next phase of existing facility management platforms. Take a light fixture as an example, Since the contractor and the supplier already entered the associated data such as the warranty dates and manufacturer through the Digital Twin, the Operator can easily see when the warranty is ending without digging into piles of documents and files.
Ideally, Digital Twins should be created at the very beginning of a project, with GCs collaborating with the Operators to understand what information is important to monitor and what should be captured in the Digital Twin for future reference.
Digital Twins can even exist in the Design phase, although from what I have seen it has yet to be used widely. But conceptually there are benefits like creating Digital Twins of the surrounding area to understand how much foot traffic there is on the street surrounding the site and more.
Benefits for Construction
In Construction, Digital Twins can have many benefits. Two key ones are:
Safety – you can put sensors on various site machinery (i.e. a crane, an excavator, etc.) and include them on the digital construction model. You can simulate scenarios and evaluate safety before actual activities happen on-site. You can also set up security alerts sent from the digital twin platform to the responsible person on-site.
Logistics Monitoring and Project Tracking – creating Digital Twins using real-time sensors allows us to have the most up-to-date information and get a better picture of the schedule in a visual format. For example, utilizing concrete sensors to monitor curing time.
What Digital Twin Software is Out There?
In my opinion, there is a race to be the best Digital Twin software as there is no stand out leader. Many are claiming their software is providing a Digital Twin; however, it might provide only one or two components of the concept. Some of the big platforms include Autodesk Tandem, Bentley iTwin, Hexagon, and NVIDIA Omniverse.
Challenges and How the Building Industry Can Get Ahead
I believe the industry’s unreadiness to adopt Digital Twin technology is our biggest challenge. Industry awareness and guidelines, at least in Canada, are lacking today. In turn, clients lack an understanding of what Digital Twins are.
The building construction industry will be impacted heavily by generative AI. In fact, tech startups are already gathering data from us. In the future, this could allow a mass data dump, and automatic pairing of data with the different assets in the model. Once this happens, the aforementioned handover from GC to Operator process will be not just seamless, but it will be automatic. It will become much more efficient, and companies need to adopt these practices before we fall behind.
Recommendations for Companies: To get ready for the digital twin future, I suggest:
-
Embrace a digital-first approach
-
Begin digitizing processes and centralizing data
-
Closely work with people and develop digital process before selecting technologies
-
Be willing to try out new technologies
Companies shouldn’t be afraid of concepts like Digital Twins – they should embrace them. They open doors to many exciting and beneficial future opportunities.