Transforming construction through sustainability and Lean practices
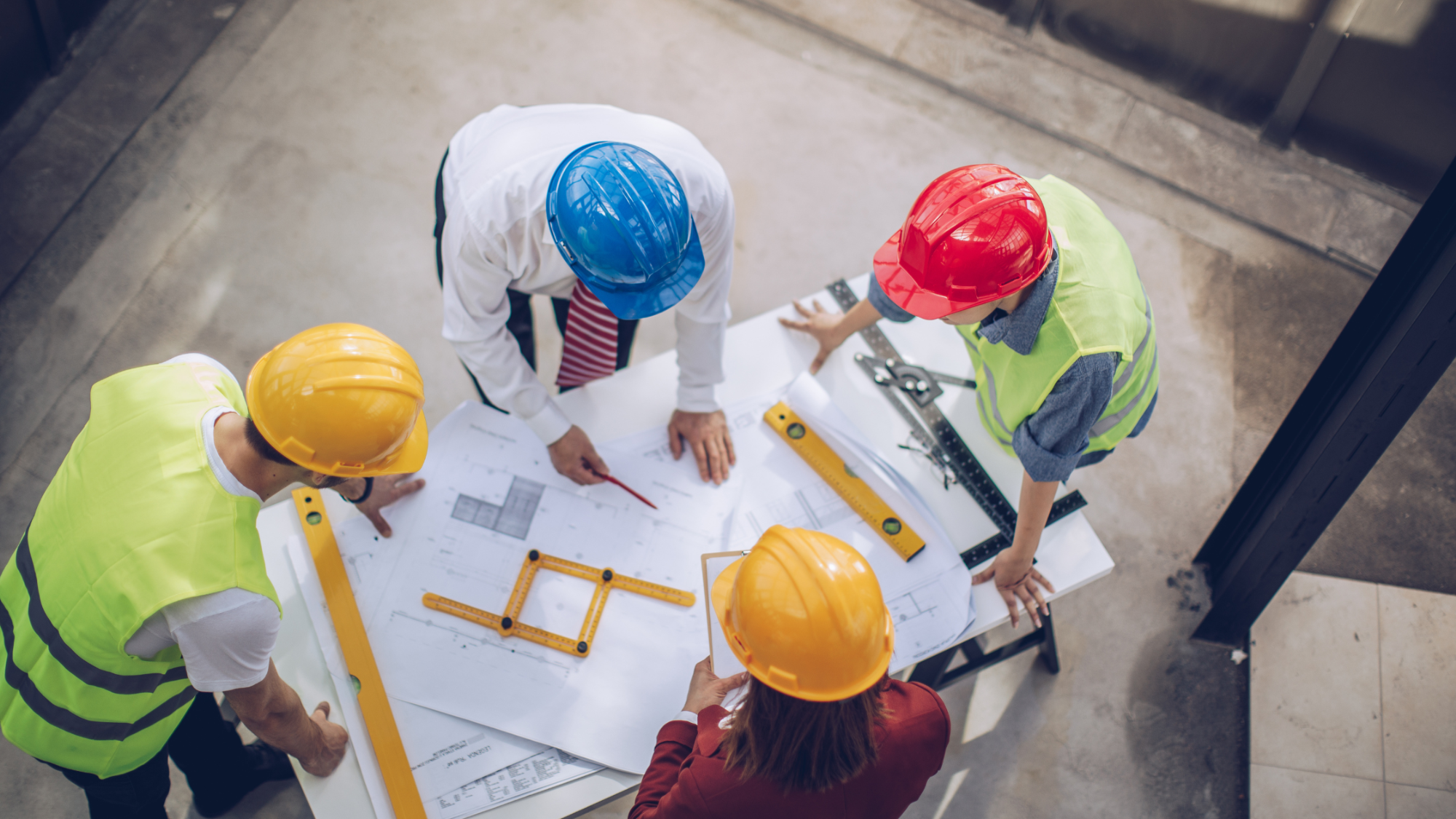
Throughout the course of my career, I've often been involved with projects across the United States pursuing sustainability goals like achieving LEED (Leadership in Energy and Environmental Design) certification, and in the latest part of my career I’ve seen an increase in the presence of Lean Construction (Lean) in addition to LEED across projects.
There is a mutual connection between Lean and LEED as many project teams may include some LEED Accredited Professional (APs) or LEED Green Associate team members, both of which bring strong industry knowledge to their teams and projects. LEED APs complete 30 hours of continuing education every two years and LEED Green Associates complete 15 hours every two years. Attending conferences, workshops, or completing online lessons, this ongoing education enables easier team collaboration among clients, design professionals, and builders, keeping up with changes in the standards and industry.
Lean practitioners also have various learning options, from informal on-the-job training to structured certification programs. Here is a shortlist from searching the web:
-
Certificate of Management - Lean Construction (AGC CM-Lean)
-
Agile Certified Practitioner (PMI-ACP)
-
Lean Six Sigma (LSSI Academy)
-
Lean Construction Institute Certificate Courses (LCI Training)
-
Scrum in Design and Construction (Scrum Inc. Course)
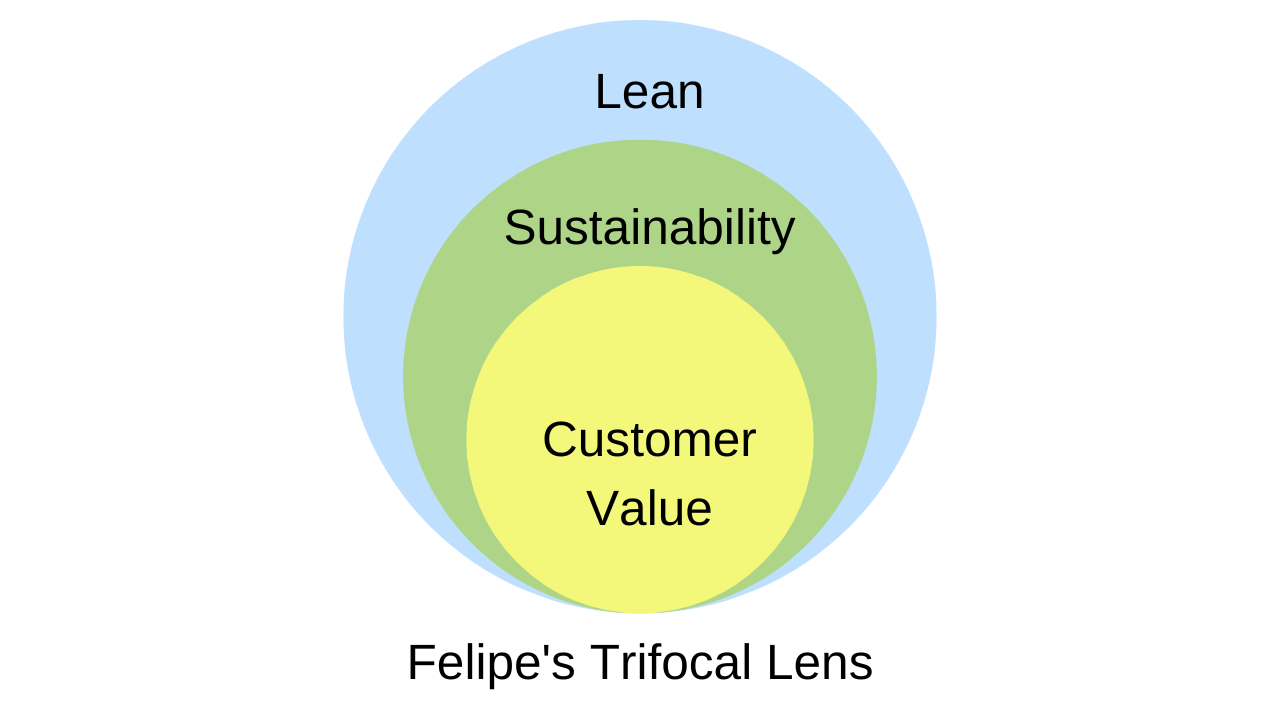
With the increase of Lean Construction practices and requirements across projects, I often hear similar questions from people. Let’s have a look at some these questions.
Where did Lean come from?
Lean is the term coined to describe the management philosophy and practices made famous by the Japanese automaker Toyota. Credit for “Lean” as we use it today goes to John Krafcik, who was part of the research team responsible for the book The Machine That Changed the World authored by James P. Womack, Daniel T. Jones, and Daniel Roos.
According to Mark Graban, Krafcik said, “[Toyota]… is “lean” because it uses less of everything compared to mass production – half the human effort in the factory, half the manufacturing space, half the investment in tools, and half the engineering hours to develop a product in half the time. Toyota also requires less than half the average inventory on site, achieves fewer defects and produces a greater and ever-growing variety of products.” Lean continues to describe the methods and thinking of Toyota most commonly. Read Mark's original post here.
Jeffery Liker authored The Toyota Way, which summarizes years of direct research describing the principles and practices at Toyota that sustain it through continuous learning by solving problems with the people closest to the issues. Toyota’s members work to deliver customer value while minimizing waste. A key principle of Lean organizations includes respect for people, both their value creators and customers, and organization-wide applied Lean principles significantly impact how customer value is created and delivered.
In summary, Lean is a learning mindset derived from sense-experience centered on a deep respect for the value of people.
What is Lean thinking?
Lean embodies a mindset as explained in Lean Thinking: Banish Waste and Create Wealth in Your Corporation. A Lean perspective frames the set of processes that deliver a project, especially its goals. Lean practitioners focus on the big picture from the context of customer/stakeholder value and non-value-adding work. Anything that doesn't support a project’s goals, doesn’t add value and warrants minimization or elimination. Lean practitioners are problem solvers working beyond the limitations of the “just another job” mindset. This approach empowers people to continue creating more customer value and drive the Lean mindset.
What does Lean mean for the construction industry?
Lean Construction often starts with adoption from an individual project team and grows toward organization-wide implementation, with culture guiding the speed and ease of adoption. When assisting a team with integration of Lean into their projects, I look to examples of Lean Construction principles.
-
Respect People
-
Deliver Value
-
Create Flow
-
Remove Waste
-
Continuously Improve
-
Optimize the Whole
In my experience, these synergistic values enable teams to deliver work easier, better, and faster. I also actively encourage and coach teams on Lean tools that promote continuous improvement with a focus on the Last Planner System of Production Controls, A3 Thinking/Problem-Solving, and Scrum. Resistance vanishes with my enthusiasm and the team's recognition of improved collaboration, communication, better team experiences, and learning.
Lean is not a tool, task, or extra work. It is a mindset of continuous learning.
I also often receive questions about sustainability principles, and how/if they intersect with Lean Construction. Some of the questions I receive include:
What are sustainability principles?
The construction industry directly impacts local and global environments. We live, work, and play on one planet and we are responsible for serving as stewards of the environment entrusted to us for the next generations to follow.
Sustainability principles include:
-
Respect people and planet
-
Deliver value
-
Create flow
-
Remove waste
-
Continuously improve
-
Optimize the whole
Environmental sustainability means that pollution creation, and non-renewable resource depletion don’t continue indefinitely and that human social and economic actions work in harmony with the environment.
Sustainability has evolved in business to describe how organizations and people impact the environment positively and negatively. These environmental impacts refer to the people processes involved in materials/resource utilization processes such as manufacturing and construction. Buildings change the local environments throughout their multi-decade operations and international supply chains invoke sustainable thinking beyond the physical building location.
Therefore, sustainability principles can significantly impact resource use to efficiently make and operate buildings for people living in communities around the world.
Do Lean and sustainability intersect?
Yes. Sustainable construction practices center around environmental issues that affect people. Lean Construction principles start and stop with people. The ideas are not mutually exclusive; rather, they are complimentary. A sustainable building project may or may not include applied Lean principles. Likewise, a Lean project may or may not include sustainable building practices, although high-intensity Lean projects often do.
A connection through respect
In my experience, Lean and sustainability principles are interwoven through the focus on increasing customer value, improving flow, decreasing waste, and continuously improving, all of which builds greater respect for project stakeholders. Lean is ultimately about people transforming their work, not just making projects more efficient and sustainable – however, those are often results of continuously improving their work. Trying to improve how you build, how sustainably you build, or a combination of both equates more respect for people and the planet and a more sustainable industry as a whole.
Content repurposed from Felipe’s original blog “Five Most Asked Questions About LEED and Lean", originally published on August 17, 2021.