Build smarter, not harder- with Jaimie Johnston
When car companies build a new car they don’t reinvent the wheel, and they don’t have engineers assembling each car individually. Pretty much everything in our lives is built out of other smaller components that are prefabricated with some degree of automation. Except for buildings. Jaimie Johnston from Bryden Wood has been working on changing that for over 25 years and he’s had a lot of pushback, but this way of working could reduce costs by a third, reduce the impact on the environment, and make for safer workplaces. It could even help solve the labour shortage while getting underemployed people into work.
Jaimie Johnston [preview]:
Everything we’re seeing tells us that we’re using less material, less transport, fewer people, you know, less operations. You know, it’s the embodied carbons collapsing. The quality of the building is improving. The running cost is reducing. The future flexibility you can design in. So all of it says that, you know, sustainability, we’re only going to address it through doing some of the—these sorts of techniques.
Tim Coldwell:
This is Building Good. I’m Tim Coldwell.
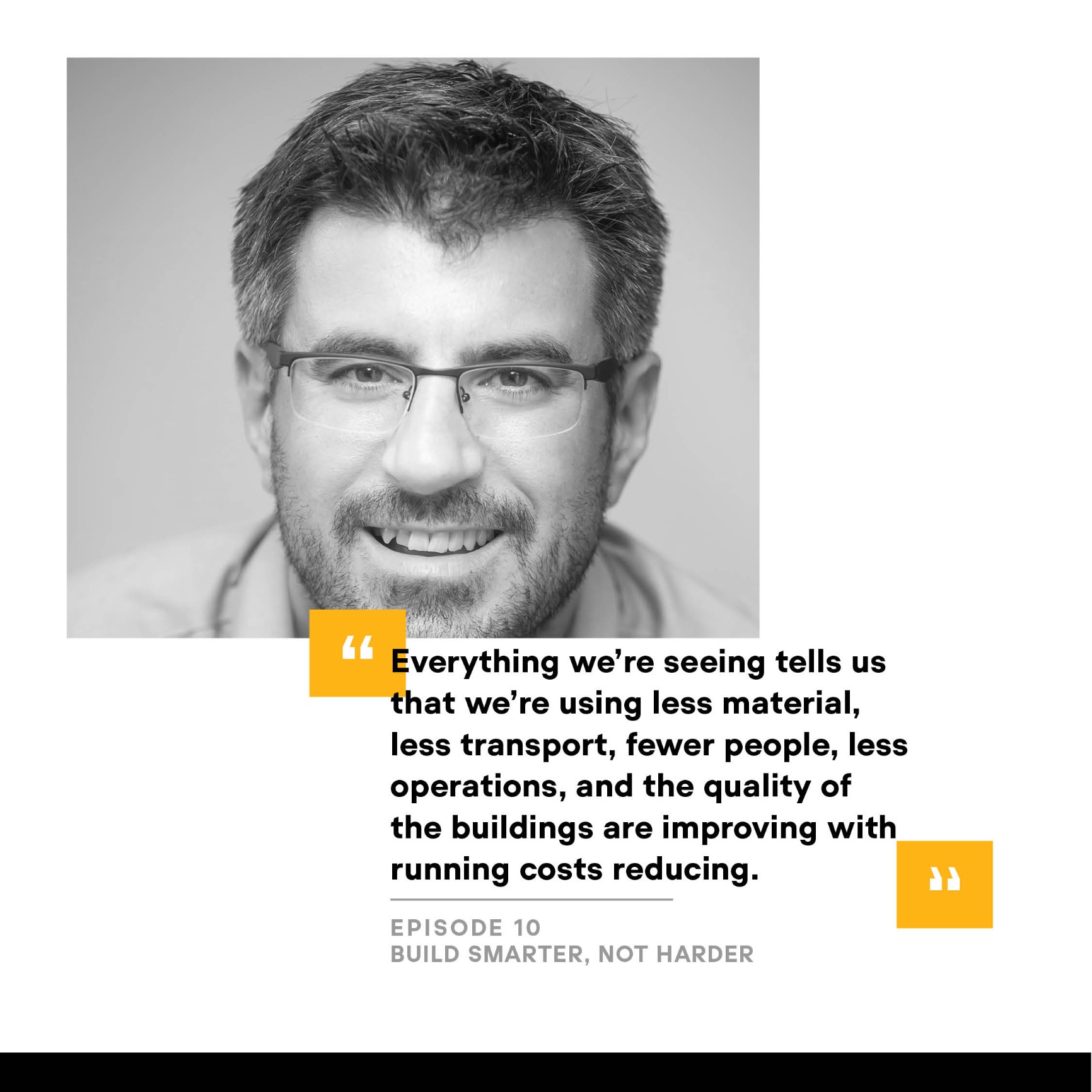
Tim Coldwell:
Construction is expensive, and labour-intensive. And there’s a real shortage of skilled workers in the industry, especially in the more specialized trades. And it’s only going to get worse as older tradespeople retire.
But there is a way to massively reduce the amount of people needed on a construction site. The same method can also reduce the cost of a project by a third, and make it more environmentally friendly. Heck, it can even help rehabilitate offenders serving time in prison.
It sounds like a ‘magic bullet’ for an industry that has a lot of problems to deal with. So why doesn’t everyone use it?
[music]
Tim Coldwell:
This magic bullet is called “platforms.” And Jaimie Johnston has been pushing for this to be used in the industry for over 20 years. And it really does do all those things I talked about. And that’s part of why it has been such a struggle to get the industry onboard.
Jaimie is going to explain it better than I could in a minute but, in short, it’s a process of standardizing the parts of construction that are pretty much the same across all kinds of projects.
Jaimie is the head of Global Systems at the design firm Bryden Wood. And over the last two decades-plus, they’ve been creating repeatable designs and publishing them, open source, for free. Every client they work with joins them in this process. As they work on each project, they see designs that can be reused elsewhere.
But words like “cookie cutter” get thrown around. And fewer people on-site means fewer jobs. As you’re going to hear, though, neither of those complaints really stand up to scrutiny.
Before we get to that decades-long struggle, I think it’s best if Jaimie himself explains how he designs for a manufacturing-led method of construction.
Jaimie Johnston:
What we do has evolved quite a lot over time. Why we do it has been fairly persistent. So, polymetric modular is typically making a building-sized piece of building in a factory somewhere—so making, you know, half a classroom, or half an apartment, or certainly a bathroom pod or something. So it’s literally kind of, one-to-one. It’s the size of the thing it will be on-site, but it’s just it’s made in a factory, typically put on the back of a truck, brought to site, and craned in.
So what it means is you don’t have many people on-site, and you’re working in sort of potentially factory-like conditions. So it’s safer, and it’s more productive, and you’re not in the wind, and rain, and things. So it’s certainly a step forwards.
What we’ve seen, though, is it does have some downsides. So quite often when you go to the modular manufacturing facilities, I wouldn’t describe it as manufacturing. It’s sort of it’s more like construction in a shed. And you know, that’s better because it’s not construction in the rain but it’s not manufacturing.
So the things that manufacturing does, there’s a sort of scale that manufacturing works at that we simply can’t replicate in construction. Even the big pipelines don’t need millions of things in the way that, say, automotive plants do.
So it comes with certain problems. You also tend to make the volumetric unit stiff enough for lifting and shifting. But in its final position there’s too much structure in it, and you’re going to actually have introduced some cost in carbon, and transport miles, and a bunch of other things. But again, if you’re sort of trying to maximize value, you’re going, “Well, there must be a better way.”
So we started to say, “Well, actually, buildings are mostly air. The bits of interest (audible, 3:56) are the bits that sit between the volumes of air. So I want say, a classroom to be, you know, nice proportions, really the bit I want to manufacture is the bit that sits in between that block of air and the next one—either in the walls, or the ceilings, and things.
So we started looking more at the components than trying to do—rather than trying to do an entire school or entire classroom in a factory—saying can I just make, you know, the floor unit, and have all the mechanical-electrical systems in that? Make it as a cassette. You know, I can fit loads of those on the back of a truck, and therefore I’m much more compact; I’m really starting to manufacture these components but I’m starting to use, ah, a greater efficiency on-site.
So the platforms thing came out of having developed lots of these solutions for lots of different clients, saying there’s actually loads of commonality between lots of building types. So for instance, floor-to-floor heights are set by people; they’re not set by sector. And a sort of person-sized floor-to-floor height, you can get natural light eight metres into a building. That’s why schools and hospitals and apartments they have the same kind of span characteristics—because they’re all based around people.
So we started saying if you looked for that commonality and really enhanced it, you could identify kits of parts that could be used across multiple sectors. The sort of mental picture maybe is IKEA—that, ah…. You know, if you buy at IKEA—whether it’s a wardrobe, or a chest of drawers, or a bookshelf, or whatever—the kits of parts are various often the same connectors every time; the book is always the same. Let’s do that for buildings. What’s the IKEA kit of parts for buildings? So that’s where, platforms thinking. But it came out of, you know, having developed loads of different systems, for loads of different clients, and saying, “Well actually, we’re starting to see some common themes here. Could we lean into that rather than focus on the difference for individual clients?”
Tim Coldwell:
Well, let’s just talk about there’s a labour crisis in the construction industry. There’s ageing infrastructure. When was the last time you talked to a 13-year-old kid who wants to be a plumber or an electrician? This way of building buildings somewhat is a solution to a labour crisis. What are your thoughts on that?
Jaimie Johnston:
Yeah. It’s one of the things that’s been particularly attractive to the U.K. government. So the U.K. government has picked up this platforms concept and it’s now sort of enshrined in, ah, government policy over here.
But we did something for Heathrow Airport, 2004. So that was a volumetric product. It was post-9/11; we had to separate out arriving and departing passengers. So we had to build—I think we built a kilometre-and-a-half of pier buildings. So incredibly repetitive. It did make sense to do it very much off-site because of the constraints of working airside in a live airport. That’s really a place where you do want to get people off-site.
But we set up a manufacturing facility that was, I would say, close to being proper manufacturing. But we designed the building as a kit of parts and assembly process. And we literally got unemployed people from the local job centre, trained them how to assemble the components. And literally some unemployed people who had never worked in construction built a chunk of airports. And even they were going, “It wasn’t actually that hard.”
Automotive does this very well. It’s not mechanics and engineers that build your car. It’s people that have been trained to assemble the components in a particular way.
So what we found that’s, I think, interesting is if you get construction people to put these things together, they’re kind of looking for the problems. They’re looking…. They try to catch you out and going, “I’ll find a bracket that doesn’t fit. I’ll find a thing that, you know…”
Tim Coldwell:
(laughing)
Jaimie Johnston:
“… I’m going to have to hit with a hammer eventually.”
Tim Coldwell:
(laughing)
Jaimie Johnston:
(laughs, inaudible) Whereas if you get a non-construction person who doesn’t know that’s not how you build a building, they go, “Yeah. It seems entirely sensible that the orange bracket goes there, and a bolt. And I’m going to drop this bit in, and then put the yellow bracket on. And yeah, that seems like a pretty sensible thing to do, to me.”
So we found sometimes having non-construction people is quite beneficial because they don’t come with some of the sort of baggage and some of the, ah, maybe bad behaviours or bad habits that come from construction sites.
And then we recently did one of the first versions of platforms we developed for our Ministry of Justice. And we got a team of serving prisoners to build the prototypes. They weren’t like building cells they could put like chisels in and things they could break out. They were building components that were then assembled. But what we found was, ah, the level of engagement was through the roof. You know, they were quite interested because they knew they were doing something a bit unusual. So they were coming in in the morning with process improvements and going, “Now, I was thinking about this overnight” or “We were talking about that over dinner, and we think this would be a good way of doing it.”
So again, it firstly showed that there was a sort of a willingness of people to get involved. Ministry of Justice obviously want to rehabilitate people. So they’re saying, “If I can train up serving prisoners and teach them skills around this, and they’re more likely to get employment off the back of this because, you know, there is a market for them to do this work, then yes.” Forgot the kind of cost-saving—the impact on rehabilitation, and people’s lives, and families’ lives, and all those things would be enormous. So suddenly the government is going, “I see where you’re going with this. And if we could, you know, massively diversify construction’s workforce, we could get, you know, unemployed, and serving prisoners, and former prisoners, and ex-army, and ex-military and train them up, and they could be building schools, and hospitals, and housing, then yeah, bring it. Solve a massive problem. Create an entirely new market. What’s not to love about that? Let’s—let’s go.”
Tim Coldwell:
Yeah. Now, there’s a strong connection here to…. In Canada, with social procurement, government is viewing social procurement as a means to get folks who need a chance a path towards a high-paying career in the construction industry; and at the same time we have a labour crisis. And so certainly platforming is something that addresses both of those things.
I just want to, before I shift to the trials and tribulations of doing something new, ah, I want to unpack the idea of vertical integration and controlling all the supply and the materials versus local materials. I think this idea of are we going to order components from overseas or are we going to make them locally—with local labour and local materials—I think that’s a really important part of making platforming successful. Can we dig into that a little bit?
Jaimie Johnston:
So we found that in U.K. pounds—apologies but—if you buy a fabricated steel frame it’s about £2,500 a ton. If you buy raw steel from a steel fabricator manufacturer it’s about £800 a ton. The thing you wanted was the £800 a ton performance but you pay for it to go from the manufacturer, to a stockholder, to a fabricator, to some specialist to have every bracket bespoke welded and designed, and then it comes on-site and artisans put it together, and you get—you get a steel frame. But what we found is that you’ll then—you can buy the steel direct from the big manufacturers and then the brackets, once you’ve designed them and like, super-optimized them—done all the kind of, you know, finite element analysis and any effect analysis that you can possibly do—you get it right, that bracket we know works, the digital file I can then send to anyone to make the bracket.
So what we’ve actually started doing is buying the kind of commodities—the concrete, the steel—direct from the big manufacturers, who in some cases are bigger than the contractors, you’re going… actually they’ve got more money, they’ve got deeper pockets, and they’re a more financially stable outfit than some of the contractors, which is quite interesting. You can then source the brackets from anyone who is, you know, the closest place that can laser-cut. So someone used the analogy in the U.K.: there’s probably one sort of big steel-frame fabricator per major city, but there’s probably a little fab shop in every town; and we’ve literally been going to the little local fab shops saying, “Can you make these brackets?” Quite often they’re not construction people. They couldn’t make you a steel frame. But they know how to laser-cut and laser-weld, they’re going, “Yeah, I can make hundreds of them. We’ll just leave the thing running over the weekend. And you know, they will be stacked up in the morning.”
So our supply chain becomes big, stable commodities providers, very small local SMEs, and then—then I’m sourcing things locally, I’m keeping the investment very local, and then I’m buying, you know, the big commodities from the big existing supply chain. You know, that’s a much more, again, socially sustainable model.
So again, you join all these bits up and, you know, aside from there’s, you know, cost-savings and productivity, you go actually the, you know, that’s a potentially really powerful way of engaging a whole load of new people in construction and, yeah, properly making that shift into a more kind of manufacturing-type.
Tim Coldwell:
There’s got to be an impact on the planet. Just talk quickly about reduction in carbon footprint using a platforming approach versus a stick-built approach.
Jaimie Johnston:
So because of the repeatability of the components, you put tons more effort into designing them than you would ever do on a kind of one-off building.
We’ve got a project for a company called Landsec, which is the U.K.’s biggest developer. It’s on site at the moment. It’s independently verified. We’ve got 20 per cent less embodied carbon in the—the super-structure than you would traditionally. It’s their first Net Zero building. Because of the way we’ve designed the structure and mechanical-electrical systems to be sort of very compact, so we don’t have the kind of slab and then a zone for pipes, and a zone for ducts, and a zone for cable track and a zone for—and you end up with, you know, massive ceiling voids, which drive up the volume of the building, and then you have to heat and treat that air, so you need bigger air-handling units and things—because of this sort of making things more compact whilst building in kind of future flexibility, we could actually generally get a reduced building volume but more of it’s usable. So we’ll get lower floor-to-floor heights but better floor-to-ceiling heights. So you go so you’ve got a nicer to space to work in, in a smaller building volume, which means your running costs are lower, your air-handling units are smaller.
What we found then, on the façade, in that project is because there’s less of the kind of solid spandrel panel, we actually get more natural light into the building. So it uses less electric light.
And so we—we talk about these sort of chain-reactions of benefit. You’re going well actually in reducing the embodied carbon, I’ve actually made a nicer space to be, with better lighting and better ceiling heights.
And it seems weird that, you know, we sometimes get pushback from people about manufacturing in construction, they go, “Aww, it just means everything is going to be cookie-cutter.” And you go, “No, no, no. Nothing else in your life is like that.” You expect everything else to perform better. You expect now all of your electrical appliances to have a rating telling you how energy-efficient they are. We should do the same for buildings. Everything we’re seeing tells us that we’re using less material, less transport, fewer people, you know, less operations. You know, it’s the embodied carbons collapsing. The quality of the building is improving. The running cost is reducing. The future flexibility you can design in. So all of it says that, you know, sustainability, we’re only going to address it through doing some of the—these sorts of techniques.
Tim Coldwell:
So let’s talk about how it’s hard to do really innovative things. And when I first got introduced to Bryden Wood, I get this immediate sense they’re kind of kindred souls, so to speak, between our two organizations. And Chandos has been a leader in Canada in, ah, advocating for and driving change with the adoption of integrated project delivery.
And I remember all the pushback, and all of the eyerolling, and “This doesn’t work.” And—and just to kind of recap, what I heard from the business case, let’s call it, for platforming: the promise of 30 per cent lower cost; the promise of 30 to 50 per cent, ah, less people on the job site; the ability to engage a wider cross-section of people in the supply chain and give them meaning and purpose in their work; and address social challenges at the same time; 30 per cent or so faster schedule; and 20 per cent less embodied carbon. And it’s not exactly like they’re lining up around the street for this kind of work.
Jaimie Johnston:
(laughs)
Tim Coldwell:
So let’s talk about that.
Jaimie Johnston:
Architects used to have enormous fees. And they were protected by the Royal Institute of British Architects. So it was almost like a mandatory: you pay an architect, you pay them this fee. And it gave architects the luxury of having the sort of the time and the money to be the master builder, understand every aspect of a project. And then in the kind of the big recessions in the sort of ‘80s/‘90s, they stopped being protective fees and become sort of recommended fees. And then they stopped being recommended and it was—it was like every architect for themselves.
So that started a trend of architects, particularly, and then the other disciplines I would say followed, trying to kind of limit their scope actually, and saying, “Well, I only want to do these bits.” And so what we’ve seen, certainly in the U.K., is that architects, firstly they tend to work in particular bits of a project. So you get concept architects or executive architects. Or we’ve worked on projects where there’s been a concept architect, an executive architect, interiors architect, façade architect. That even the architectural role has been atomized.
And then people tend to work in, say, sectors. You know, you’ve got people looking at only one part of a project, in one discipline, in one sector. They’re only seeing a kind of tiny part of the whole problem.
I’ve got a slide I sometimes use that shows quite how many disciplines you now need to have a project. And it’s gone from being sort of, you know, architect and a few others to hundreds of consultants. So firstly, all the gaps in between them are where all the problems are. It’s all the kind of misinterpretations; it’s all the missing information. They’re typically, for good reasons, trying to sort of defend a particular bit of the project, but they don’t want to go outside of it because maybe their insurance doesn’t cover it and they’re going “risk. The more things they take on, the more risk there is.”
So we were a kinda deliberate action. So if we did all of that, owned the entire puzzle, then all of those gaps disappear. So going to that was one of the big steps. We go, “We need to be much, much better integrated, because the only way we’re going to start to do these is to think much, much more wholistically.”
You know, we sort of did the opposite of everyone else and said, “No, no. We’re going to take on more, and more, and more, and more of the understanding of the complete ecosystem of things.” But that whole thing of, you know, being super-integrated, trying to own more of the problem and not get rid of the risk and sort of try and bat it on to other people. Being very, you know, we publish everything. We open source all the apps and things.
So trying to share what we’re doing, people instantly find a bit suspicious. They’re going, “You’re up to something.” And we’re going, “You know, we’re trying to make the world a better place. We’re not transforming construction.”
Tim Coldwell:
(laughing)
Jaimie Johnston:
[And they would go,] “Yeah, what are you really up to though?” So yeah, we just have a sort of an attitude that seems to be the opposite of, ah, lots of the rest of the industry. And yeah, that’s really hard—that people don’t understand what we’re doing or recognize, necessarily, what we’re doing. Because it’s so alien to the way that normally industry works.
Tim Coldwell:
You know, when we kind of talked earlier on, we kind of had a no-holds-barred conversation about general contractors. And I’ve always scratched my head on how few contractors see these movements by big owners and government and say, “Huh. If we get out in front of that, we’re going to differentiate. We’re going to win more business. We’re going to be seen as progressive.” Why do you think so many people dig their heels in and oppose it?
Jaimie Johnston:
Every wants to be a fast follower. No one wants to be the person who goes racing ahead into this. Because what if the client’s wrong, or what if this model doesn’t work for them? I think there’s a sort of natural reluctance to go. It is quite a shift; it is quite a disruptive thing. It will change my business model significantly. It’s not easy to do a sort of, you know, one-off little project like this. So I think there’s a nervousness because it’s quite high stakes. “Yeah, I could transform my model and I could win massively. Or I could just disappear in it.”
I think also the, ah, certainly in the U.K. the margins are so tight. But I think there’s definitely a nervousness that everyone is feeling. Yeah, the same pressures that are driving this—you know, skills gap’s a problem, certainly, you know, very recently price of materials are hiking, pipelines are uncertain—there’s so much kind of risk and uncertainty, and the profits aren’t there to sort of go, “Yeah, we could take a hit on this and be fine.”
So it feels like there’s a load of things that are coming together in that space that no one’s got the breathing space to kind of stop and think and, you know, rework themselves.
Tim Coldwell:
So let’s paint a picture for the audience. What does the world look like when the industry has accepted the Bryden Wood way of working? Do buildings look different? Like what does that future look like in your mind?
Jaimie Johnston:
So say we’ve got a series of these configurates that I talked about. We’ve got them for housing, and schools, and roads, and things. So saying it’s really plausible, actually, that if you joined them all up, you could not design sort of social infrastructure, transport infrastructure, but it could be derived from millions of simulations or iterations of testing actually what is the absolute optimum placement of built environment versus not, and where would be the transport modes.
And you could actually evidence-base how to build social infrastructure moving forward. The problem statement is how to support 11.5 billion people sustainably? And you’re done. That’s like the big question that industry needs to solve.
But you could actually plausibly drive a lot of that through simulation and analysis and evidence-based. And you’re going once you’ve done that, it would then say, “Well, here’s where you build housing at site level. Here’s the optimum, you know, footprint of housing, and the best massing of housing to get the best energy balance, and views, and light, and, you know, social, ah, return, and all the rest of it.”
And then, “This is the kit of parts you’ll need to build that stuff.” And then that self-orders to a supply chain of people who put their hand up and say, “Yeah, I’ve got capacity to do these.” And then autonomous vehicles deliver this stuff. And then robots assemble it on-site, say, with very few people. And then it’s all equipped with IoT that self-optimizes the buildings. They adapt themselves over time to enhance productivity, and health, and well-being. And you get this sort of, you know, self-sustaining, self-building, self-optimizing social infrastructure that’s there to benefit humankind. You go, “Yeah, that’s really plausible. We could do that.”
I think if we don’t do that then by the time we hit peak world population, we’ll—we’ll have killed the planet before we hit peak population. We can’t possibly build enough schools, and houses, and healthcare and transport infrastructure for another four billion people that are on the way—at the current rate of doing things. So you go, “Well, there is a plausible way of not killing the planet. Or carry on, see how we get on. But, you know, your grandkids won’t hate you because they’ll be dead.”
It sounds a bit stark when it’s that sort of, ah…. Yeah, the stakes are massively high on this. But luckily, there’s all the bits in place, I think, to transform how we think about our built environment.
[music]
Tim Coldwell:
That was Jaimie Johnston, head of Global Systems at Bryden Wood. Thanks for checking out this episode with Jaimie. Hopefully, more people like you will hear it and take note. And we can help make construction more efficient and find our way out of the labour shortage.
Hit the “Follow” button, so you don’t miss more Building Good. And if you like what we’re doing here and want to help us build good, leave a rating or a review, or just tell a friend about the show. It helps other people find us, and those reviews are always fun to read.
Building Good is a Vocal Fry Studios production. The executive producer is Jay Cockburn. Our associate producer is Kattie Laur, with production assistance from Jessica Loughlin. I’m Tim Coldwell. Thanks for listening.