Teaching old wood new tricks w/ Eric Law
Wood isn’t what it used to be. Virgin lumber is generally less dense and grown faster than wood that was harvested from natural old growth forests. But logging what’s left of those old growth forests isn’t a sustainable option, so why not reclaim old lumber when buildings are torn down? Until now that process was labour intensive and expensive, but Eric Law and Urban Machine have developed robots that are making reclaimed lumber into the building material of choice, and that might just change the way we build new buildings entirely.
[sound effect]
Eric Law:
We call it “The Big Ugly.” It’s about 150 feet long. The humans are loading wood onto these custom designed porcupine rollers. We’re removing structural fasteners, electrical boxes, plumbing pipe. The humans take those off, and then they feed it into the first of four machines.
Geoff Capelle:
This robot, and the humans that feed it, might be the reason new buildings start to look very different.
Eric Law:
The first machine cuts all the heads off all the fasteners, and gets us really to a rectangular shape of wood so we can process it better.
[sound effects]
Geoff Capelle:
If The Big Ugly gets what it wants, then eventually we will be surrounded by recycled wood—not just in single-family homes but in tower blocks too. And we won’t have to cut down trees to get it.
[sawing noises]
Eric Law:
Then that machine pushes it into the second one. And what that second machine does is then it goes and cooks all those fasteners. And by cooking the fasteners, what we’re doing is we’re turning screws essentially into a nail. When I cook it, what I end up with is I char the wood and the threads. And so I can pull the whole screw out, just like a nail.
Geoff Capelle:
Eric Law is the CEO and founder of Urban Machine. And it’s their robot you’re hearing him describe.
Eric Law:
And then after we cook it, we pass it through to our next process, which is the picker. And so that’s where the cameras come into play. They take pictures of it. They identify the fasteners, and then they pull them out. We’ve affectionately called it The Bird, because it uses like a bird beak to dig into the wood and pull out the fasteners.
Geoff Capelle:
This robot is taking an expensive boutique material—reclaimed lumber—and making it an affordable construction resource. Instead of an expensive process of manual labour, which might create a nice mantel for a fireplace, the robot can churn out enough material to actually build things. Where we used to throw out the majority of wood from a demolished building, Urban Machine reuses it—turning trash into tower blocks.
Eric Law:
And then from there, the last step we run it through a metal detector. And that’s where we check to make sure we got all the metal out. And then it heads out. And the humans are sorting and racking it up to get loaded on the trucks.
Geoff Capelle:
This is Building Good. I’m Geoff Capelle.
[very brief music]
Geoff Capelle:
Wood has a long history in construction.
[music]
Geoff Capelle:
In North America, it’s one of the main materials used to build single-family homes. If I walk down one of the leafy residential streets in my city of Toronto, I can see wood everywhere—even on the red brick Victorians. It’s in the eaves. It’s what the porches and decks are built out of.
But there’s very little wood that’s over 40 feet from the ground. Look up and all you see is glass and concrete. That’s a problem.
[music]
Geoff Capelle:
Cement and concrete are responsible for eight per cent of carbon emissions, globally. As Rob Cumming said, in an older episode of Building Good…
Rob Cumming:
There’s more concrete sold than all other building materials combined. In fact, we believe it’s the second highest consumed material, second only to water, globally.
[music]
Geoff Capelle:
So there’s good reason to minimize the use of concrete. And we’re seeing more projects using new mass timber technologies to build with more wood. But wood isn’t perfect.
Vast swaths of British Columbia are dedicated to growing trees rapidly, and then cutting them down. That timber is processed into lumber. Then you have to transport it. And at the end of a building’s life, it probably gets thrown out or incinerated.
It’s better than cement but it’s not ideal. And those rapidly grown trees are nowhere near the quality of lumber that’s sitting in older buildings waiting to be thrown out when they’re demolished.
Eric Law:
Reclaimed lumber is one of the few recycled materials where it’s actually higher quality than the virgin one. Right? If I take a two-by-four from a lumber yard today and I compare it to a six-month-old, there’s really not a big difference. But if I compare it to a piece of material that’s, say, 60 years old, that 60-year-old material has a lot less knots, a lot tighter grain; it’s a much higher quality piece of material.
Geoff Capelle:
Eric showed us what it looks like when you cut through a piece of timber and compare it to old-growth wood. You can see difference.
Eric Law:
On the top, you’ve got maybe 50 to 100 rings per inch of diameter. And then on the bottom, you’re 10 to 20 rings per inch. And so that gives you a really good idea of how faster the trees grew, and how much younger they were when they were harvested.
Geoff Capelle:
So why not take that old lumber and reclaim it, and reuse it in new buildings? That’s what Eric Law and Urban Machine are doing. And if they get their way, reclaimed lumber will be the building material of choice.
[music]
Eric Law:
Wood is a beautiful product. It’s a natural product. It’s got a much warmer texture to it. It makes a really nice finish. And what’s happened is the mass timber technology that’s been imported from Europe into North America is starting to gain traction here in the U.S. And that consumes a lot of lumber, ah, a lot of wood from the forest to create those mass timber projects.
Unfortunately, the sustainability side of mass timber involves they use a lot of glue, which really hurts the sustainability characteristics of mass timber.
The cool thing about wood is it stores carbon—compared to steel and concrete that generate a lot.
And so if you look at it from an environmental perspective, you have a beautiful product that’s more sustainable until you glue it all together, and then it makes the recycle path really hard.
And so what we’ve done is we’ve developed technology to say, “Hey, let’s make wood even more sustainable. Let’s keep it out of the landfills. Let’s keep it out of the incinerators.” Because as long as you keep it dry and bug-free, it’ll last thousands of years. It’s a phenomenal natural product; grows pretty quickly in the forests. We can harvest it, build with it, and reuse it multiple times. That’s the goal that we’re doing.
Geoff Capelle:
And what makes wood more sustainable than cement and steel?
Eric Law:
A couple aspects of it. One is the wood grows in the forest and as it’s growing in the forest, it’s absorbing carbon from the atmosphere. It also cleans the air—pulls pollutants out of the air. Generates oxygen. It’s a huge…. Right? Trees are huge benefit to humans, for human health. It provides habitat for the critters and stuff like that. And then you can harvest it and continuously harvest it, right, like a farm product.
And then when—after you harvest it, the process is much lighter on the energy footprint than when you think about concrete and steel. Right? Concrete and steel involve mining, and then processing. And they involve massive amounts of energy in that processing. Neither of them actually store CO2. Wood is the only structural building product that actually stores CO2 in its fibres.
And so with wood, you have a lighter processing footprint compared to concrete and steel. And then you can bring it through, dry it out, and then put it in buildings. So it’s essentially a carbon sink, right?
Now, concrete and steel, what they’re doing to make their(6:39) more sustainable is they’re going with solar power, and they’re getting the gas out of kilns, and they’re reducing Portland cement. And so they, too, are also working to become more sustainable building materials—by reducing the energy footprint it takes to process what they do to create those products.
Geoff Capelle:
Where is all this wood that we use in the North American building industry coming from?
Eric Law:
So, it’s all virgin lumber. Predominantly it comes out of Pacific northwest—so you’re looking Oregon, Washington, British Columbia—the three primary providers of forest products to North America. And then you get the southeast with Southern Yellow Pine, (inaudible, 7:14) substantial amount. But the majority comes out of the northwest, there. And then that’s where the majority of mills are, as well.
Geoff Capelle:
And why is that a problem?
Eric Law:
So, it requires a lot of logistics. If you think about it, there’s huge populations down in Los Angeles, Dallas, Texas—they’re nowhere near the forests. So to get the lumber from the Pacific northwest down there, it’s a long train ride, truck ride—depending on what they’re using—so a substantial amount of diesel fuel. And then there’s no way to close the loop and get the recycled lumber back, unless you want to transport it again with (inaudible, 7:46) of diesel fuel. Right? So it’s a long supply chain.
And one of the things that covid highlighted was how fragile that supply chain is. You know, the mills were expecting lumber demand to go down, so they slowed down their production. And what ended up happening was demand increased—because everybody started building home offices, and remodels, and spending time at home—and lumber prices upped almost 4X at the peak there. And what that did is it created a dramatic increase in the price to build homes. It increased housing prices for us here in North America.
And even once the mills caught up, the trains and the trucks couldn’t catch up. They couldn’t get the material to the market. And then you had more spikes and more uncertainty in the market.
And so, with our process, we’re locally sourced in the metropolitan areas. So like Los Angeles, we can source material from all the buildings that are coming down and getting remodelled down there, process it, and then put it back into that market. We don’t have that long supply chain like the virgin material does.
Geoff Capelle:
So then why aren’t folks using reclaimed lumber right now? What’s the issue?
Eric Law:
Yeah. So the—it gets used kind of in a small market. So if you think about like fireplace mantels, high-end siding. You can get reclaimed lumber from like really old buildings, like barns. And the reason why they do that is because it sells for a premium. You know, if your average lumber is, you know, about a buck-a-board-foot, you know, at your local lumber yard, if you look at reclaimed lumber today, you know, you could be paying $10 to $40 a board foot. And the reason being is it’s small volumes; it’s typically processed by hand, so they’re hand de-nailing it and pulling the metal fasteners out. So it adds a labour cost to it. And then, typically, they inventory it, waiting for the customer to match that particular architectural element.
And so that’s where our goal is to change that and say, “Hey, let’s reclaim all the lumber, not just the historical stuff. But let’s go after every two-by-four. Let’s clean it up, get the metal fasteners out of it, and then get it back into the market.” Once it’s metal-free, then everybody can reuse it.
Geoff Capelle:
This reclaimed wood, is it something that could be used structurally? Or this is more for finishes? What would be the use case for it?
Eric Law:
Depending on where you are, the building codes have a couple options for you.
So in the U.S., you can use reclaimed lumber for structural applications. In Canada, you can’t use it for structural loads; you could use it for partition walls, no problem. But in structural applications, the Canadian code doesn’t allow it. The U.S. one requires it be regraded. And then we actually have two states in the U.S.—Oregon and Washington—where they’re saying all reclaimed lumber gets a “No. 2.” Because nobody puts anything worse than a No. 2 into a building. So they’re like, “Why do we have to regrade it?” Everything is 2 or better, historically, in the buildings. As long as there’s no rot or decay, you know, do a quick visual inspection, you should be good to go.
And we’re going to see there’s actually a proposal to update the Canadian building code to allow reclaimed lumber in structural use. Because it’s actually higher quality. It’s actually got better structural characteristics than the virgin stuff today.
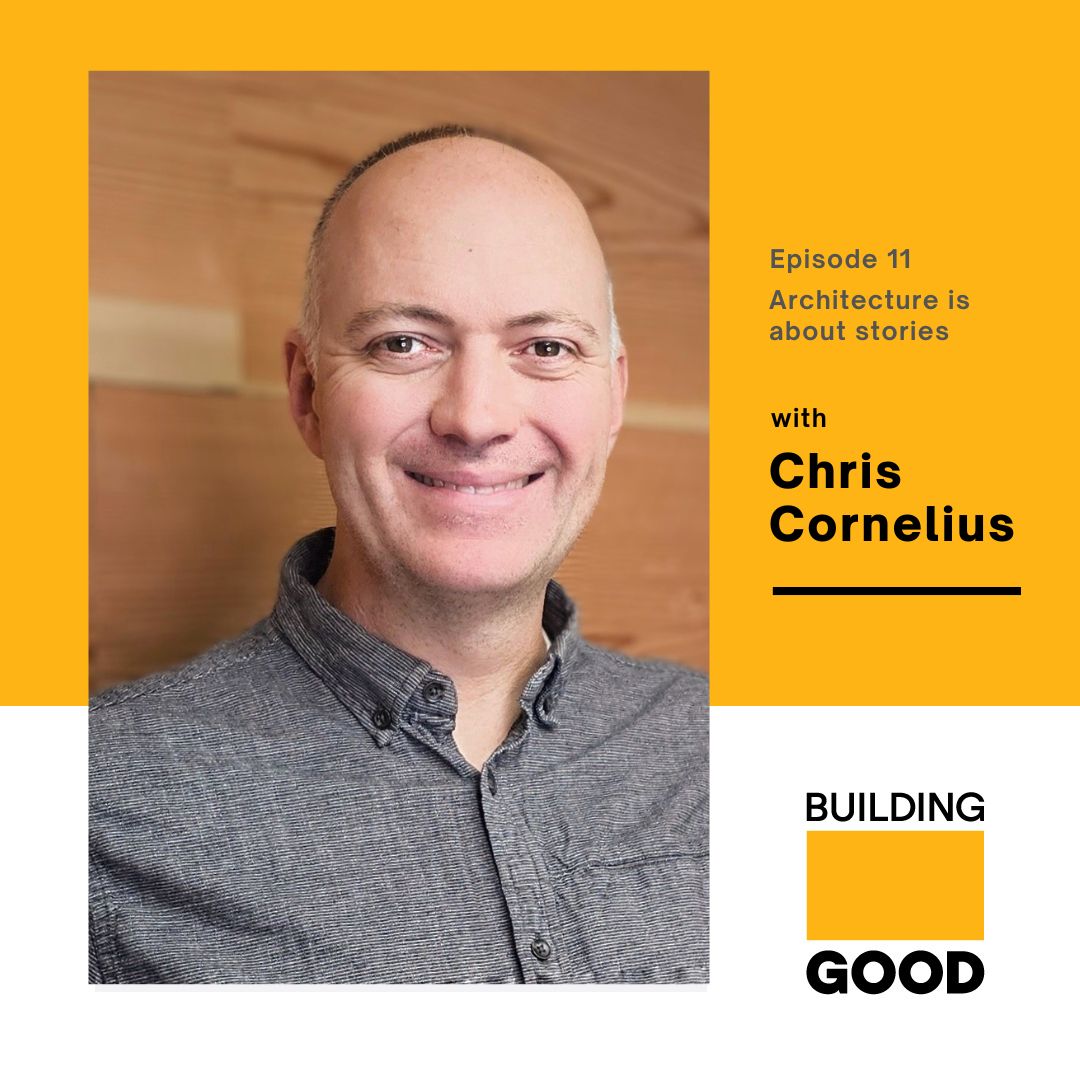
Geoff Capelle:
So, one thing I found really interesting as I was reading up on Urban Machine was that it really strikes me that, in many ways, this isn’t necessarily a construction company. It’s a technology company that’s addressing a construction challenge, in a sense. So I’m really curious about Urban Machine. Tell us more about it. Tell us about your robots.
Eric Law:
What we’re doing is we are combining construction, technology, and sustainability. And on the tech side we’re using computer vision, AI, and robotics. And what we’re doing is, the challenge with the mass adoption of reclaimed lumber is getting the metal fasteners out.
Because when the fasteners are in the boards, you can’t mill it, plane it, glue it together—there’s a lot of processes you can’t do because the metal doesn’t go through a wood manufacturing line. And so our whole scope is to get the wood metal-free. Once it’s metal-free then you can feed it into any lumber manufacture and turn that into a finished product.
And so that’s what’s really preventing wood from being recycled or reclaimed today. And so that’s what we’re focused on, is automating that process.
This is also a process that’s pretty laborious and hard on the human body. So nobody has really done this at scale, because it’s going to just be too expensive to have, you know, 50 humans pulling nails all day long [laughs a little] on an assembly line. That’s pretty hard stuff.
And in my past working with robots, you know, when somebody says, “Hey, it’s a highly repetitive process. It’s dull, dangerous, or dirty. And humans don’t like doing it. It’s like, that’s a great one for robots.” Robots are really good at highly repetitive processes. And so that’s what got us started on this journey, almost three years ago.
Geoff Capelle:
How is it powered?
Eric Law:
Yeah. So it’s 100 per cent electric. We run 230 three-phase to it. Everything—all the actuators are actually electric. We have one pneumatic actuator on the whole system; everything else is electric.
The cooking process is actually induction. So we’re using induction coils to cook the fasteners.
So our energy footprint is actually really small compared to virgin lumber processing or recycling steel or concrete.
Geoff Capelle:
And is this something where you would likely see it on a job site as they’re taking down an older building? Or would it be located close to a processing facility? Or where is it generally located?
Eric Law:
Originally, we were hoping we could go to the job sites. But at 150 feet and 5,000 square feet, it’s just gotten a little too big for that. It’d have to be a really big wood building that’s coming down.
And so we’re working with the waste processors, who currently are the collection points for all the C&D waste. And that’s where we’re going to be locating the machines, is at those existing collection points.
So this way, the waste processor can sort the lumber off their tipping floors into our machines, clean it up close to the source, and then from there sell it into the lumber market.
Geoff Capelle:
That makes sense. One thing in construction is that we never have enough laydown space. So I can understand how that would be a challenge.
Eric Law:
(laughs) Yeah. Especially when you get into the cities, right? Like Toronto and Vancouver. (laughs)
Geoff Capelle:
Absolutely.
And does this change the way that you would demolish a building?
Eric Law:
We’re hoping so. So we’ve worked with two types of contractors. We’ve worked with demolition contractors who smash it up. And we worked with deconstruction construction contractors who take the building apart.
The big thing we get from deconstruction is a higher volume and a higher quality of material that we’re able to recover.
And what’s interesting is, talking with the demolition folks is they’re like, “Prior to you guys there’s been no market for reclaimed lumber.” Right? There was no economic incentive to take the building apart. And since we’ve been working here in the Bay area, a bunch of the demolition folks have decided to start pulling material out of buildings and doing kind of partial deconstruction for larger materials, larger beams, and sending it to us because it’s less expensive. Because now they have an economic incentive to recycle the material. They’re like, “We do this for concrete, we do it for steel, we want to do it for wood. We just need a market or a value for it.”
And so it’s awesome to hear that. It’s like the people want to do the right thing, they just need the economics to pencil out for them. Right? Like in most projects in construction, everything we do has to pencil. And so that’s what we’re doing with our technology, is we’re solving that economic challenge for how do you recycle lumber.
Geoff Capelle:
That’s great. I love hearing about how changing those economic drivers leads to behaviour change like that. That’s real transformation.
[music]
Geoff Capelle:
We’ll be back with Eric Law, and his robot, after this.
[music]
Jen Hancock:
At Chandos, building is about more than concrete and steel, drywall and windows. It’s how we build, and who we build with, that determines the legacy we leave behind.
[music]
Jen Hancock:
Our commitment to a more diverse and sustainable future is built into every aspect of our business: the people, the processes, the projects, and every community we’re part of.
Let’s build better together.
[music]
Jen Hancock:
Find out more or join our team at chandos.com. That’s C-H-A-N-D-O-S-dot-com.
Geoff Capelle:
After this process, does this make reclaimed lumber a cheap and viable construction material?
Eric Law:
Yeah. So, our goal is to compete with virgin lumber. And we want to take away the price premium that comes with reclaimed. And so this way you can get your FSC-certified reclaimed lumber at the same price as your virgin lumber—so you don’t have to pay a price premium for it anymore.
And then you can choose and say, “Hey, look. You know, I want the reclaimed lumber, I want the higher quality material, at the same price as the lower quality virgin.”
Geoff Capelle:
And I guess, part of that would be changing some of the regulations around grading in areas that haven’t been as progressive as what you had described earlier.
Eric Law:
Correct. Yeah, to get all those markets to open up for structural use. Because if you can get it into structural use, that’s a lot of demand.
Geoff Capelle:
What has interest been like on this? Are you seeing are a lot of demand?
Eric Law:
We are. We have more demand than we have wood coming out of our machine. It’s really cool. Because right now we’re still in the R&D phase; we haven’t shipped our first unit to a customer yet. So as we test the machine and we make it better, we produce clean wood coming out of it. And then we sell that wood into the northern California market where we’re operating. And then so we’ve actually got more open orders than we have material available right now. Which is a good place to be in.
Geoff Capelle:
Are you able to tell us when you’ll have a market-ready product?
Eric Law:
In October we’re going to ship our first unit to our first customer.
Geoff Capelle:
That’s exciting. It’s coming up.
Eric Law:
It is. (laughs) It is. It’s got my engineering team scared. But it’s going. (laughs)
Geoff Capelle:
Are you finding that there are some markets that are more, or less, interested in recycling materials?
Eric Law:
I would say those that are more into sustainable and have more pressure on their resources. So for example, here in North America, the west coast and the east coast where all the cities are. Right? You’ve got these dense metropolitan areas. And, you know, they don’t have the big landfills; they don’t have big(??, 17:03) waste capacity. So they typically are pushing for more sustainable solutions, to be better users of our resources but also the economics.
The cost to get rid of waste on the coasts is very, very expensive compared to folks in, like, the middle of the country. And like that range, we’ve learned, is anywhere from like $35 a ton to $200 a ton. And if you’re taking down a building and you’re spending $200 a ton to get rid of the material, that’s a big cost; that’s a big delta from 35.
Geoff Capelle:
That’s interesting. So it sort of strikes me that there might be some form of lobbying or, you know, working with governments to look at full life cycle to make this product to really increase adoption on something like this.
Eric Law:
Um-hmm. We’re seeing that in a lot of the local jurisdictions—cities, counties, and some states have started to do it, and municipalities. And we expect it to roll up into the federal agencies over the coming years.
Geoff Capelle:
Are you perceived as a competitor to some of the existing lumber processing facilities or wood operations?
Eric Law:
So far, not. They’re actually very interested in working with us. Because what we’re seeing is we’re seeing this—you kind of mentioned it earlier on—is this competition between concrete, steel, and wood. And it’s existed for a long time. (inaudible, 18:12) the lower-cost material, (??, 18:14) stronger material, better lasting. And now all three of them are competing on sustainability. Right? Who’s got the structural characteristics, the cost, and more sustainable. Which is good when they compete.
And so we are helping the lumber industry with their sustainability, in saying, “Hey, look. Now you can recycle wood. You can use it over and over, just like concrete and steel (??, 18:34).
And so, we’ve actually had some great contacts with some of your traditional virgin lumber manufacturers, who are like, “No, we want to work with you guys.” Because we close that—the circle for them.
You want to go use some recycled wood, now, are you—on your next project?
Geoff Capelle:
Oh, absolutely. I would love to. I mean, we’ve seen so much benefit in—in moving over to more wood construction. Right? Like it’s—it’s fantastic for clients. The user experience is that much better. We’re seeing much greater adoption. And it’s an area that we really look at a lot. And as we’re looking at more sustainability initiatives—full life cycle, everything—this is really compelling. I like the idea of it.
Eric Law:
Yeah. It is cool. It’s nice when you get a sustainability win. And architecturally, the designers like working with it. You know, so many—we’ve come across so many clients that are now trying to clad their steel and concrete buildings with wood. And we’re like, “Well, why didn’t you just build it from wood to begin with?”
Geoff Capelle:
Looking forward into the future, it sounds like you’ve basically taken something very niche and turned it into what could be the building material of choice. Do you see reclaimed lumber taking the place of cement and steel in the future?
Eric Law:
It’s definitely got that potential. Right? Any time you can increase the volume and decrease the price of one of the materials, you have the potential to offset demand for another one. Right?
I think, instead what we’re going to see is, as the population of the world grows and the demand for infrastructure grows, we need to make sure we have more products available to address it without increasing our mining for concrete, for steel. And so I think recycled wood is one of those opportunities to go. And we’re going to see that not just with wood but also with steel and concrete. Right? They’re going to continue to increase their recycled content.
And if we can get to a point where we no longer have to, you know, mine materials, or harvest forests, or reduce both of them, that’s a huge win. Right? There needs to be a balance. We still have to have forests, and open space, and stuff like that that’s not getting logged or mined if we’re to keep up living on this planet.
And so I think that’s where it really comes into play is, not just saying, “Hey, it’s a direct competitor,” but it’s one of our tools to reduce the need to consume natural resources.
Geoff Capelle:
How do you hope this will shape the industry?
Eric Law:
Yeah, I hope two-fold. Not just improving the sustainability of construction with this recycled product being available but to get people thinking about, “What else can we reuse?” Right? If we can do this…. You know, we’ve done it with concrete and steel, for the most part—more down-cycling with the concrete side than pure recycling—but if we can get people thinking about, “Okay, we can recycle concrete, steel, wood, what about windows?” Right? “What about all the glass in all those building facades? What about building furniture? What about the carpets? What about the drywall?”
And it's started to move to the point where we can recycle 100 per cent of the building products, that’s a huge win. And so every time we do this with a new building product, where we make it recyclable, we get closer and closer to that goal.
And as an industry, that’s what we need to keep working towards.
Geoff Capelle:
So is this next step reclaiming other materials?
Eric Law:
On our roadmap, with our core technology we want to go after sheet goods. Think about plywood and OSB. We want to go after the industrial packaging market—so think about your shipping crates and dunnage and, you know, all that stuff that holds together all the materials that arrive on the job site. That’s another opportunity.
And so we do see a lot of opportunity of recycling other components and materials that are part of the built environment with it.
[music]
Geoff Capelle:
That was Eric Law, CEO and co-founder of Urban Machine.
Thanks for listening to Building Good. We’re having conversations about changing construction for the better—through brilliant technologies like Eric Law’s robot. So if you want to be part of those conversations, stay subscribed on any podcast app.
Building Good is a Vocal Fry Studios production, in partnership with Bird Construction and Chandos Construction. The producers are Jay Cockburn and Katie Jensen, with production assistance from Jessica Loughlin. I’m Geoff Capelle, thanks for listening.
[music]